Packing for the Alaska Move
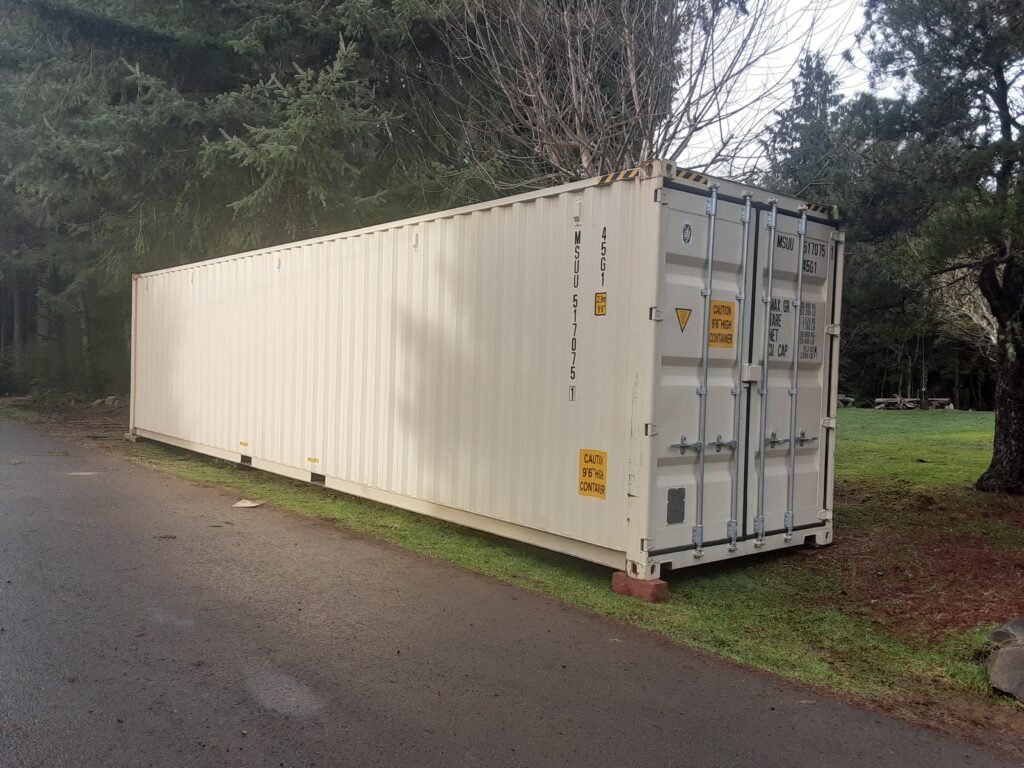
Moving is a major headache no matter how you look at it, but moving your household goods from the lower 48 to Alaska presents its own unique problems. Besides the obvious distance challenge there are other things to consider such as is some of the things that you will be moving be illegal in Canada? If you are a hunter, shooter, or avid outdoor enthusiast then the answer to that is probably yes as even empty handgun cases may be banned in Canada so that leaves only air or seaborne options. Home canned goods are also prohibited from crossing the Canadian border so it you are like us and have tons or canned tuna, clams, deer, elk, clam chowder base, and other things you will have to give all those away as you cannot take them so there are many things to consider when planning your move.
There are moving companies that specialize in moving your stuff to Alaska, but they were very expensive so we began researching other options to find a better solution that fit our needs without breaking the bank. Our house has been in our family for four generations so we accumulated a lot of usable things and memorabilia over those years. We also had a large woodshop and metal shop that had many heavy and expensive tools such as table saws, planers, drill presses, welders, and lots of other stuff. Shipping is billed per pound and shipping by land was way more costly than having your stuff barged, which is what we decided to use as it was way cheaper.
We needed a large shipping container to ship our stuff by barge using Alaska Marine Lines, which is the primary and cheapest shipper to Alaska. After many phone calls we found a 40 foot 9’6” “High cube” shipping container that they were willing to sell us for the same price as a standard 8-foot-tall shipping container so we bought our container outright. The extra 1 ½ height gave us extra room and buying it meant that we could use it for storage if needed after we bought a house in Alaska. Some places do offer rental shipping containers if you are not worried about using it for storage later. There is a rental fee from the time you get it until the time it is unloaded and returned, but it is cheaper than buying one. There were also companies that would drop off a semitruck trailer for 3 days and barge the trailer up when you are done if that works for your needs. That did not work for us as we had heavy shop equipment that would not have been easy to lift that highway. That would also mean that we would have to unload the entire thing into a storage until within three days on the Alaska side whereas we could just have the shipping container dropped off at a storage facility so we would not have to unpack it until we bought a house and started moving in.
Transportation and delivery of an empty container is straight forward and can be done with a regular pickup and long trailer, but moving a loaded one that ways upwards of 25,000 pounds will be a challenge. Unless you have access to heavy equipment or a crane you will need to find a shipping service that has a specialized side-lift trailer called a “Hammar”. The “Hammar” lifts the container off the trailer and places it onto the ground using hydraulic arms to load or unload it while keeping it level so the contents don’t fall all over. The lifting capacity is over 70,000 pounds so the only limit is what the truck can legally haul based on axles, length, and road restrictions at the time. Our container was delivered to us using a Hammar so that the driver could ensure that it was placed somewhere that he would be able to pick it up again after it was loaded up, which is important unless you are a glutton for punishment and feel like unloading and loading it again. There was ample room beside the road for our container so we were lucky.
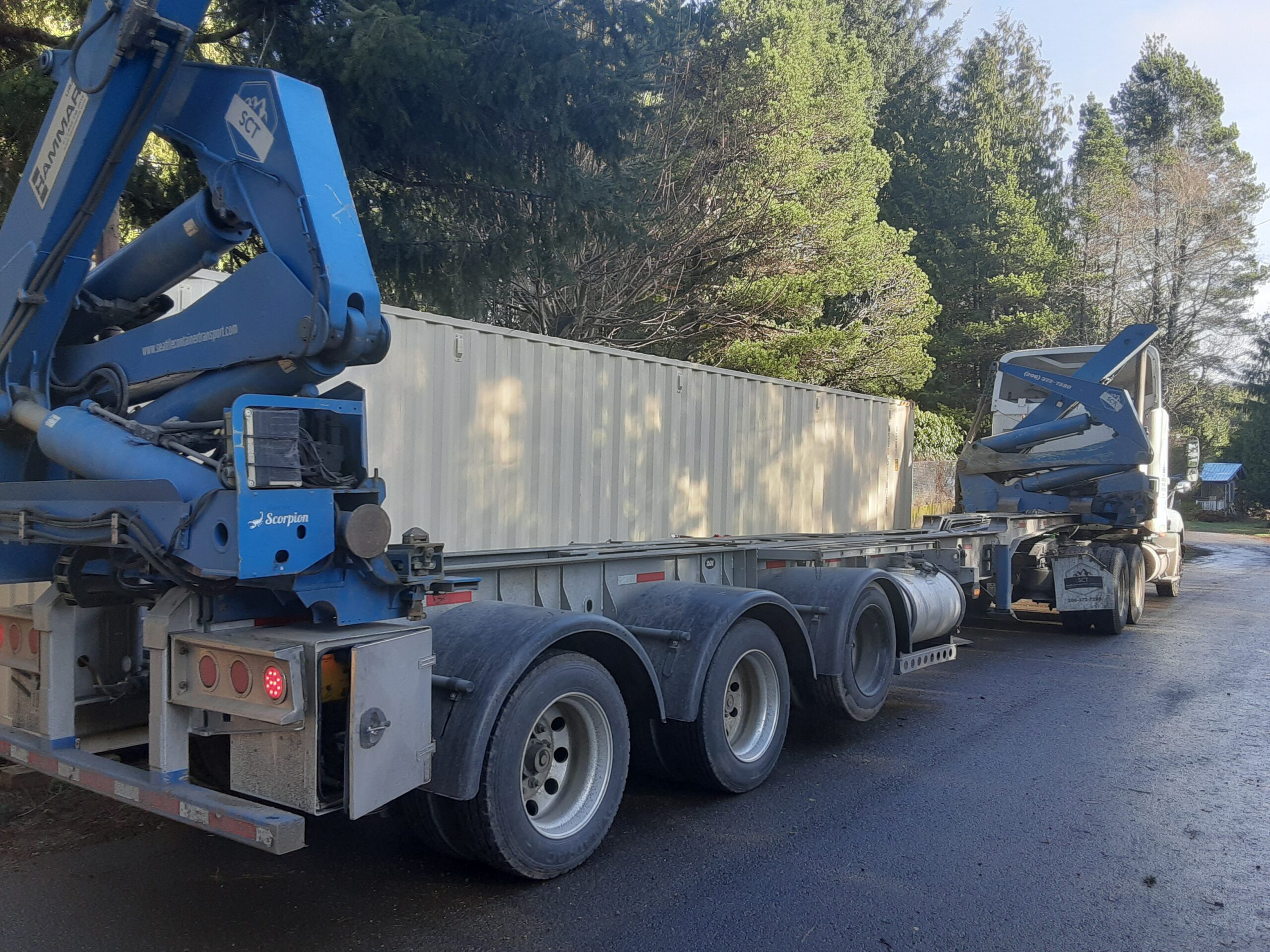
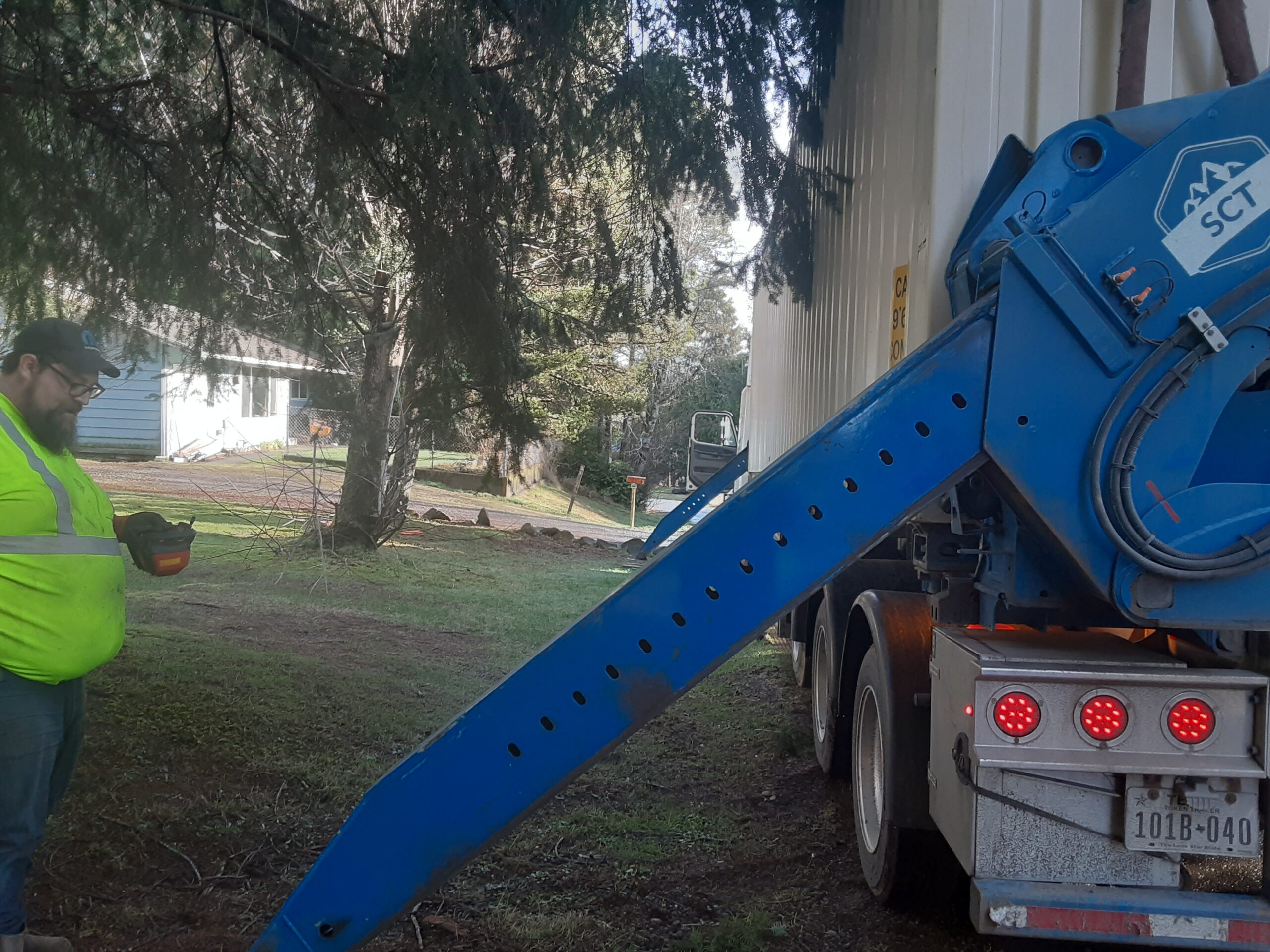
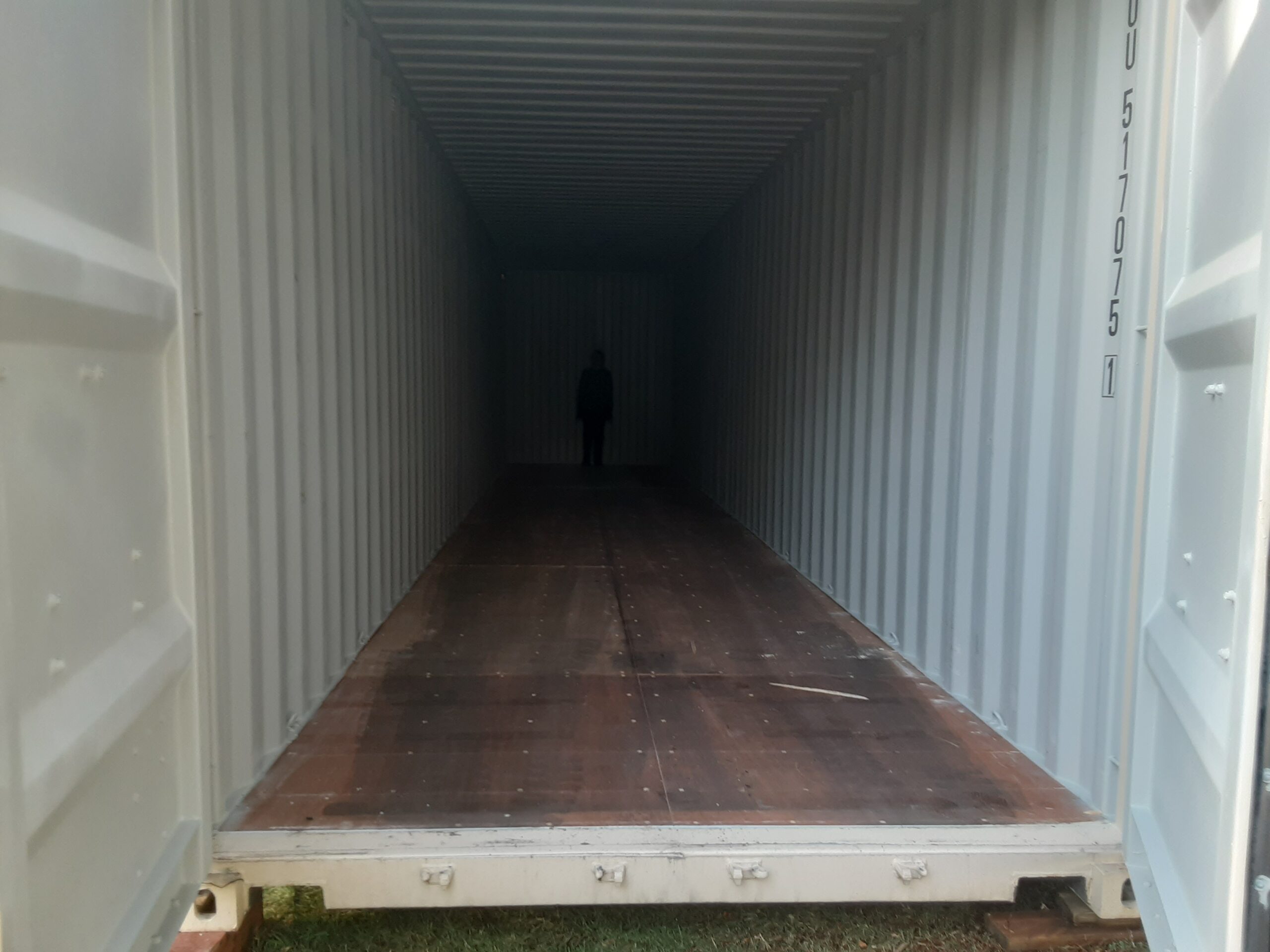
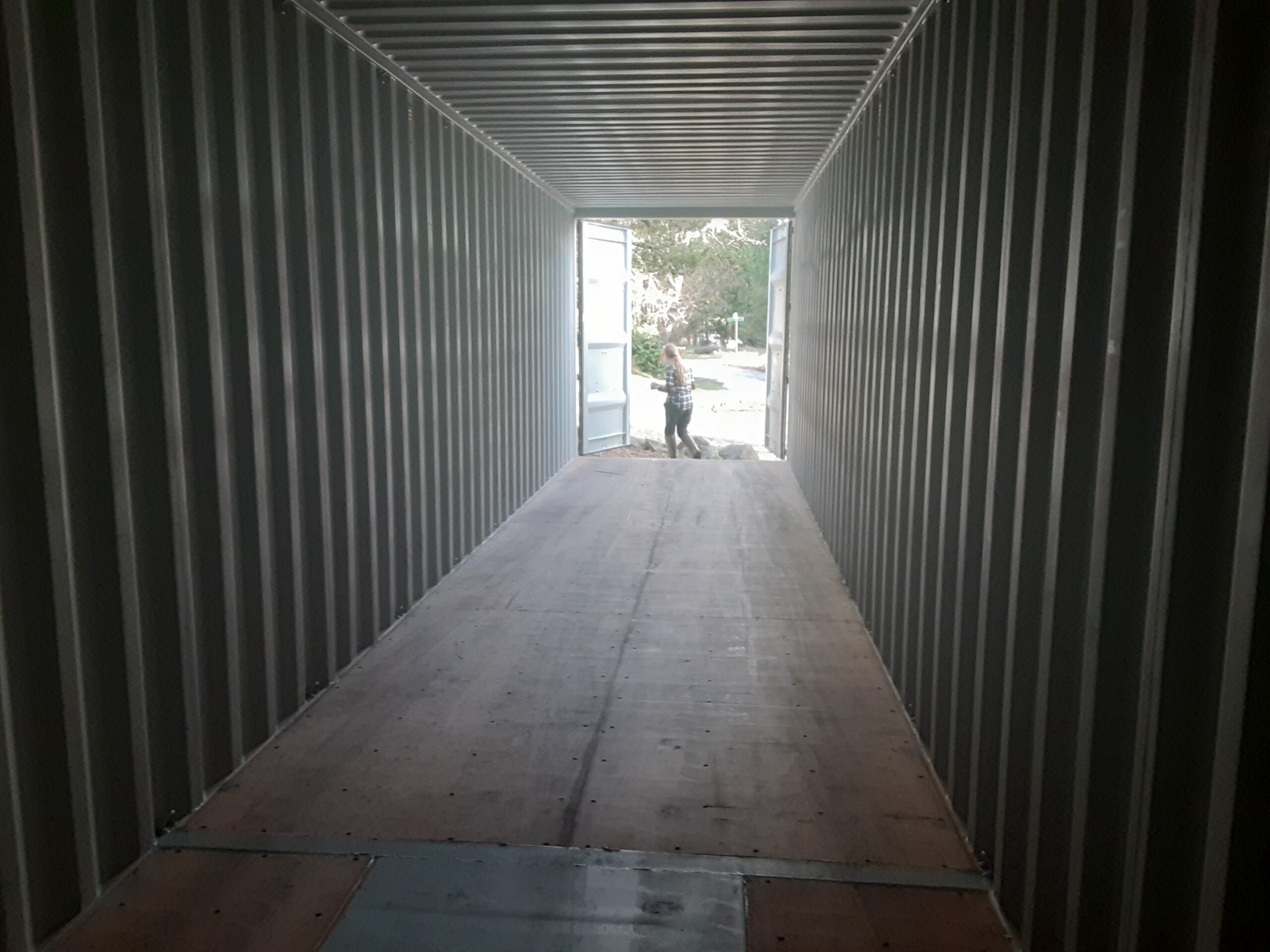
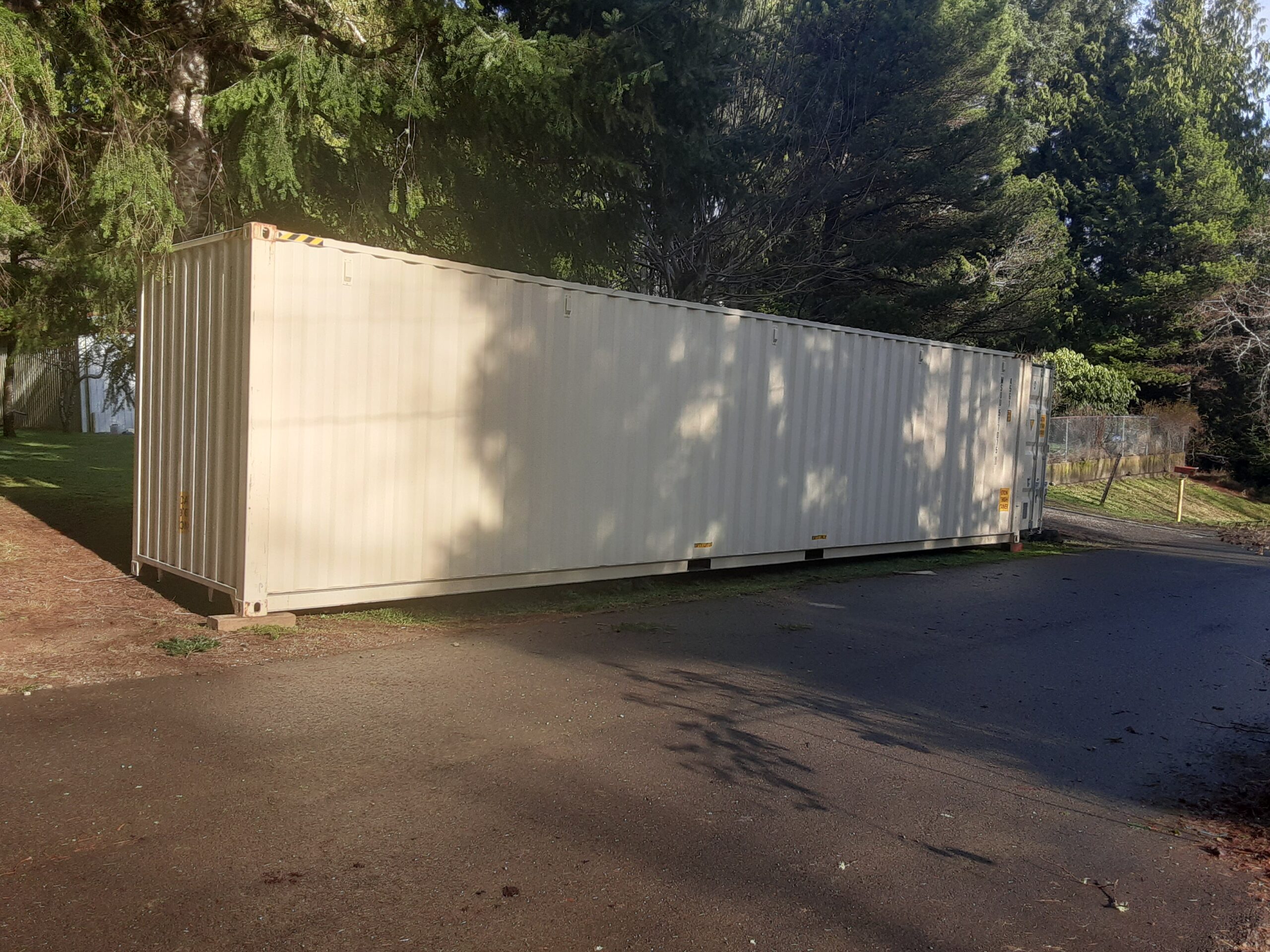
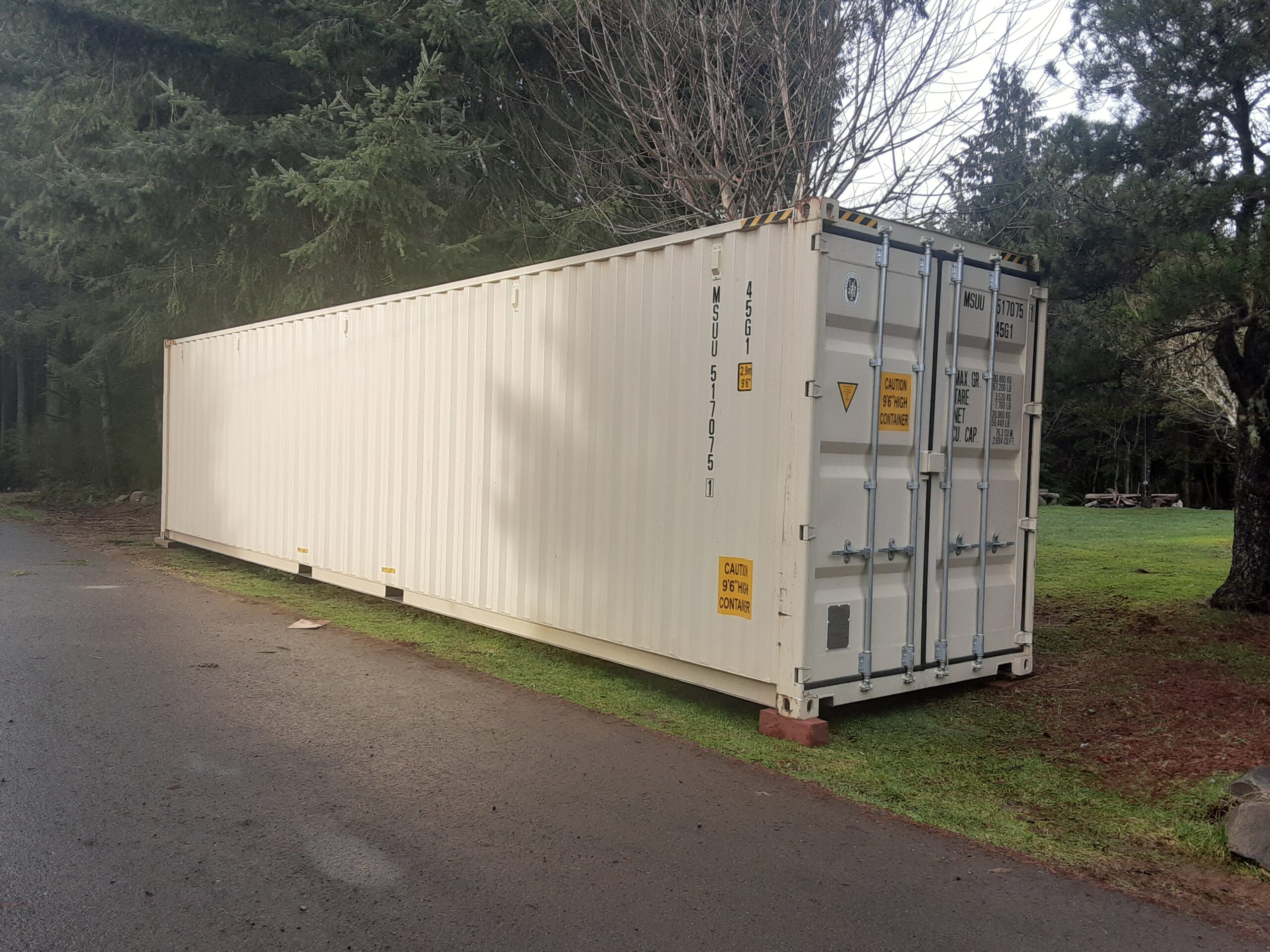
The container weight needs to be reasonably balanced so plan on spreading your heavy items out along the bottom. We used our john Deere Gator a lot during this process and put the wood splitter and gas-powered welder in first. The container had welded on loops along the top so we used a chain and hoist to lift heavy items out of the Gator after loading them using another hoist in the shop. That was a back saver and allowed the two of us to perform what would have otherwise been a four-person job. We also used the Gator as a powered wheelbarrow to haul boxes from the house so we could just back the Gator into the container to save many footsteps. Hopefully you can also find a few helpful shortcuts like this is you ever have to do this.
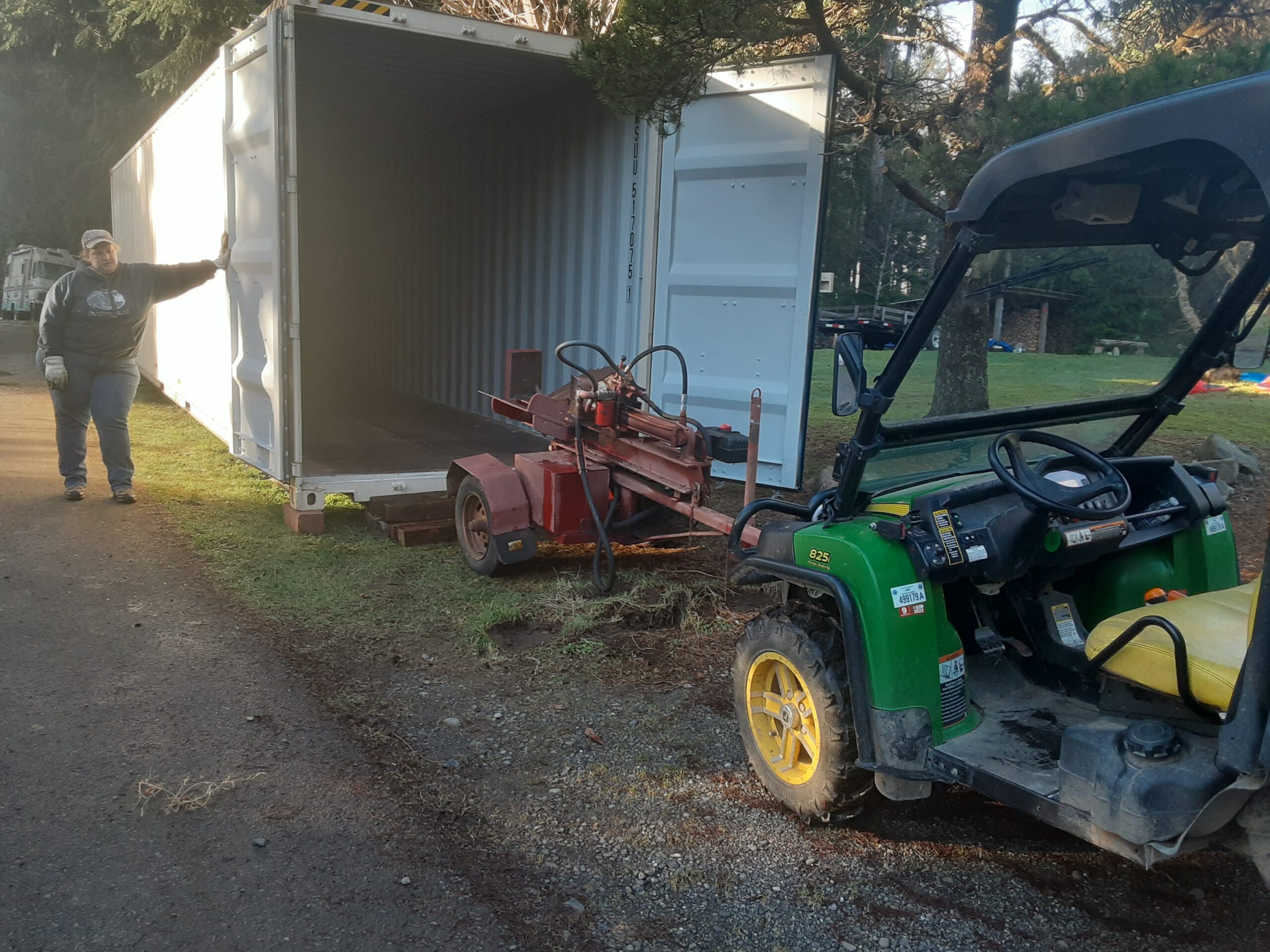
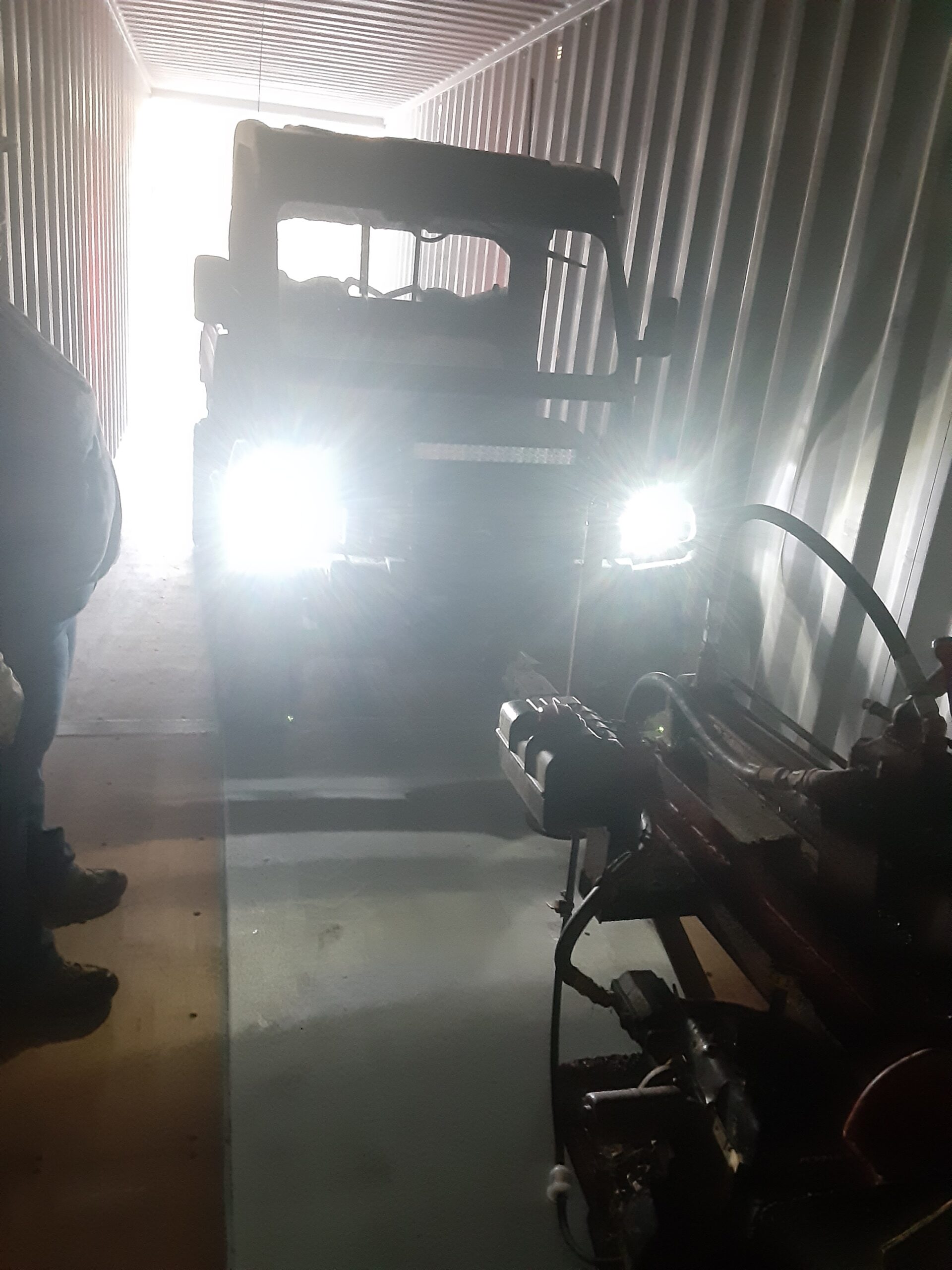
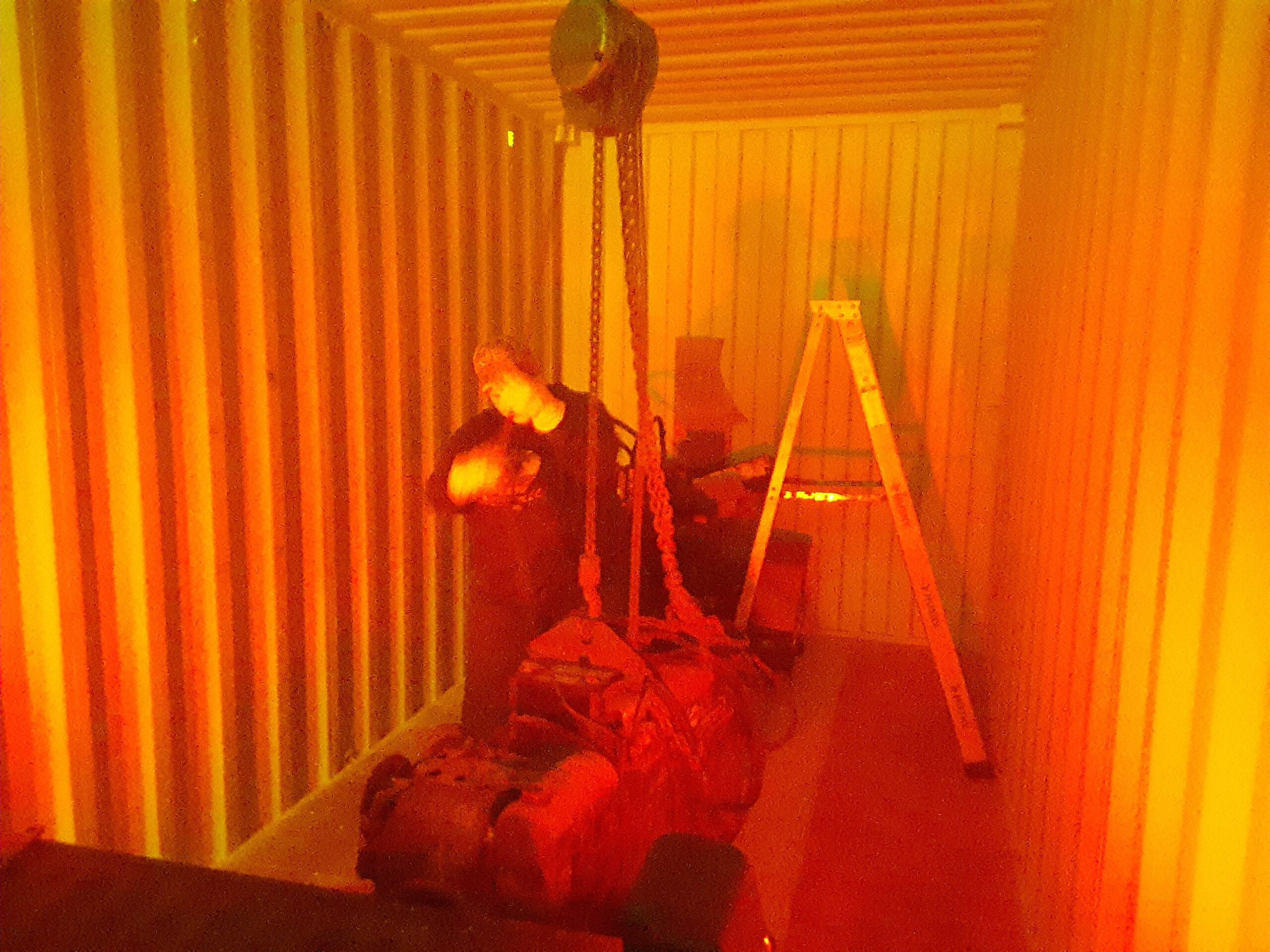
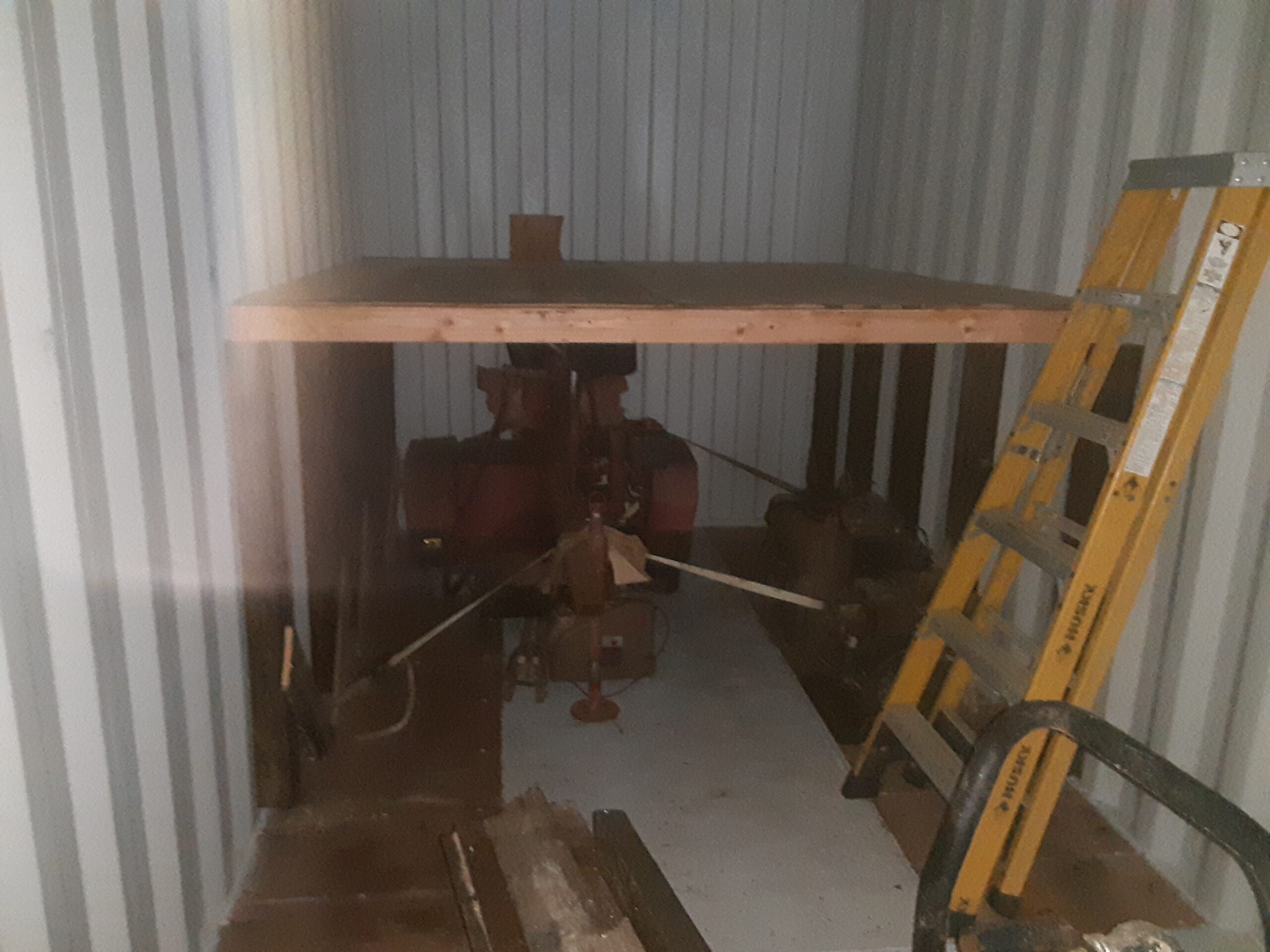
Vertical storage over odd-shaped shop equipment was another challenge as boxes are hard enough to stack high by themselves so we decided to build platforms over the equipment. 4”X4” s were cut and placed into the grooves along the walls and 2”X6” s were used to make floor joists just above the equipment so that plywood could be screwed on top of them. Everything was put together with screws so that the boards and plywood could be reused for other projects later at a new house. Cross-bracing was used to stop the posts from shifting back or forward during the transport later. Take the extra measurements and time to cut everything to fit tightly as you do not want to have a platform collapse during transit and squish everything below it. We ended up building three platforms for an additional twenty-four feet of lightweight storage above all the odd-shaped equipment. We used sheets of plywood to make baffles to prevent boxes from falling out and to stop everything from shifting too far. These platforms also provided a good brace to keep our China cabinet from falling over during the move. We spent a lot of time with a tapemeasure planning out the optimal placement of all our stuff and recalculated the space as we continued.
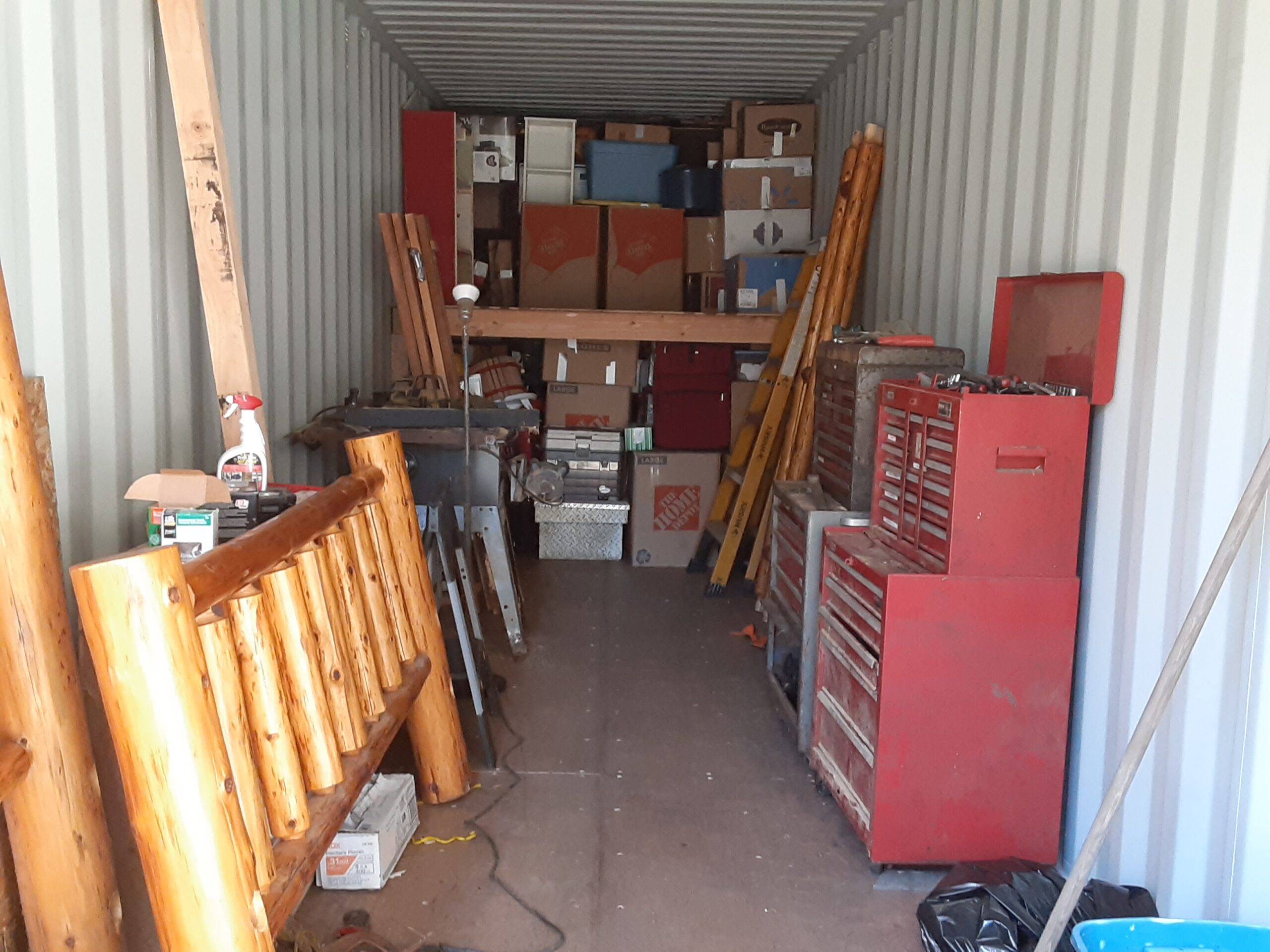
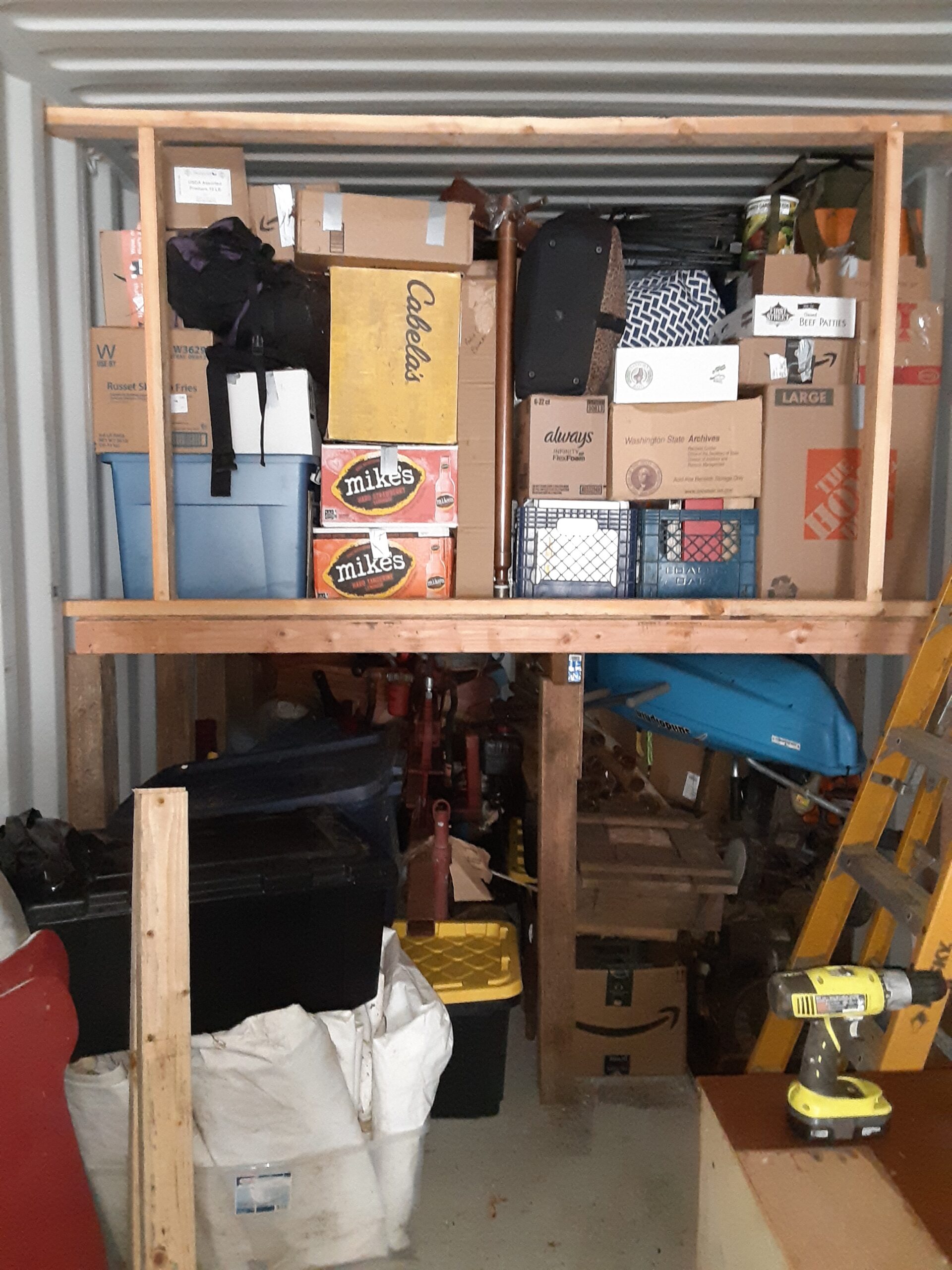
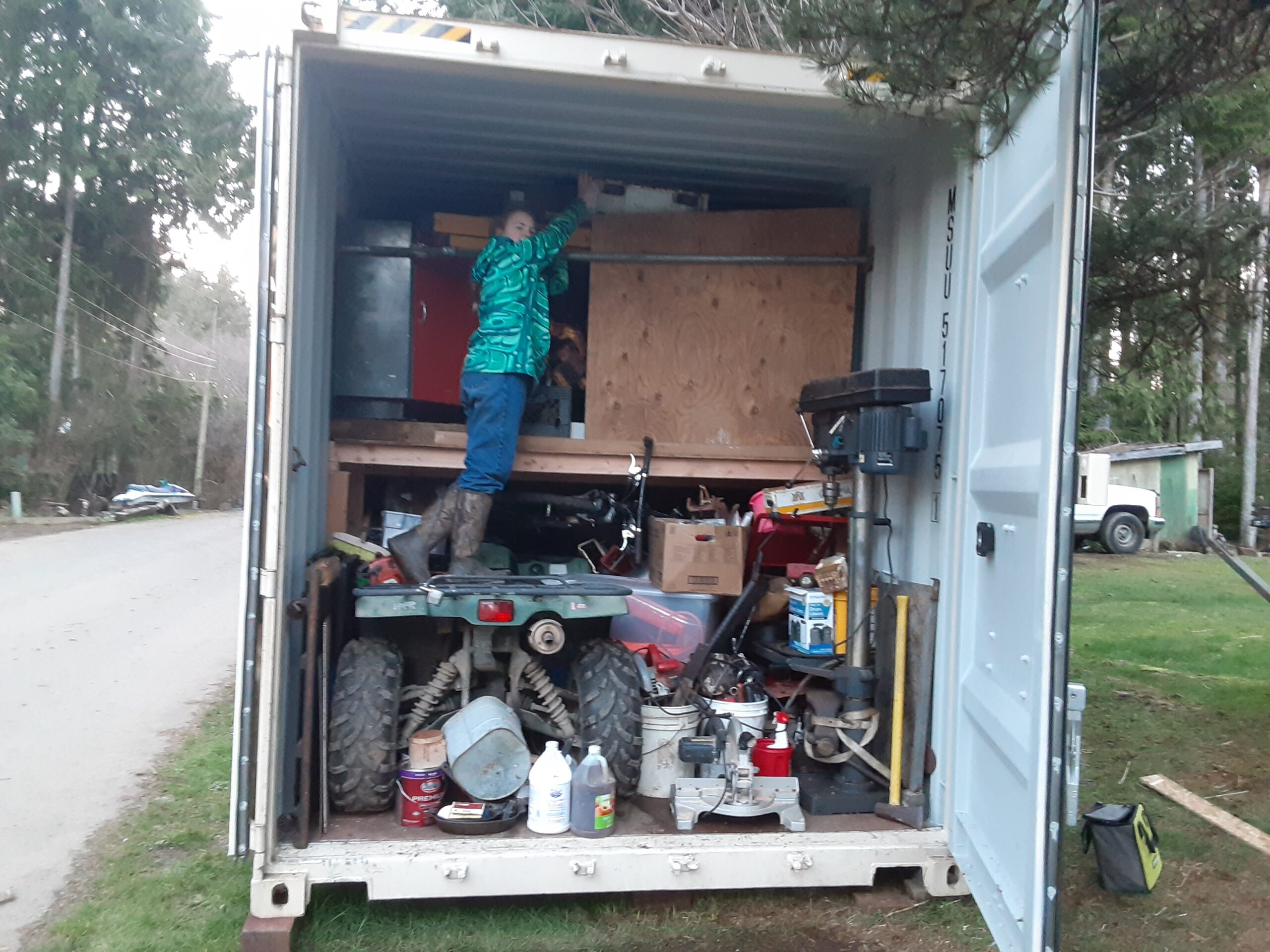
We scheduled the container pickup a few days in advance as there is only specialized truck in Washington and Alaska so allow a couple days lead time. You also need to schedule to drop off on the same or next day with the shipper so it takes a coupe calls to get this coordinated so plan ahead a few days and have patience. It took us a month and a half to sort through everything, build platforms, and pack the container so it was not easy to plan that far ahead. We had friends, family, and our church family to help us get the heavy items packed along with the final push to get everything packed so that is a blessing. The extra space also allowed us to take many extras that we would not have been able to take had we got a standard-size container. Much of that stuff was older toys, wood burls, project wood, and other things. We used more space and weight than most people would as the metal and woodworking tools took up a lot of space and weight by themselves. We did save room for one quad so we didn’t have to try to carefully pack that on the car trailer to make the trip across Canada and the Alaska Highway.
It took two-weeks for the container to arrive in Anchorage Alaska from Seattle Washington so do not be in a hurry for it to get there, even though that is a fast time considering the distance and logistics involved. The container was taken to the Alaska Marine Lines where it was placed onto a barge when there were enough others to make a load. From there it went to Whittier Alaska where it was offloaded and placed onto the Alaska Railroad train to haul into Anchorage. Offloading in Whittier is faster and cheaper than towing the barge all the way around directly to Anchorage.
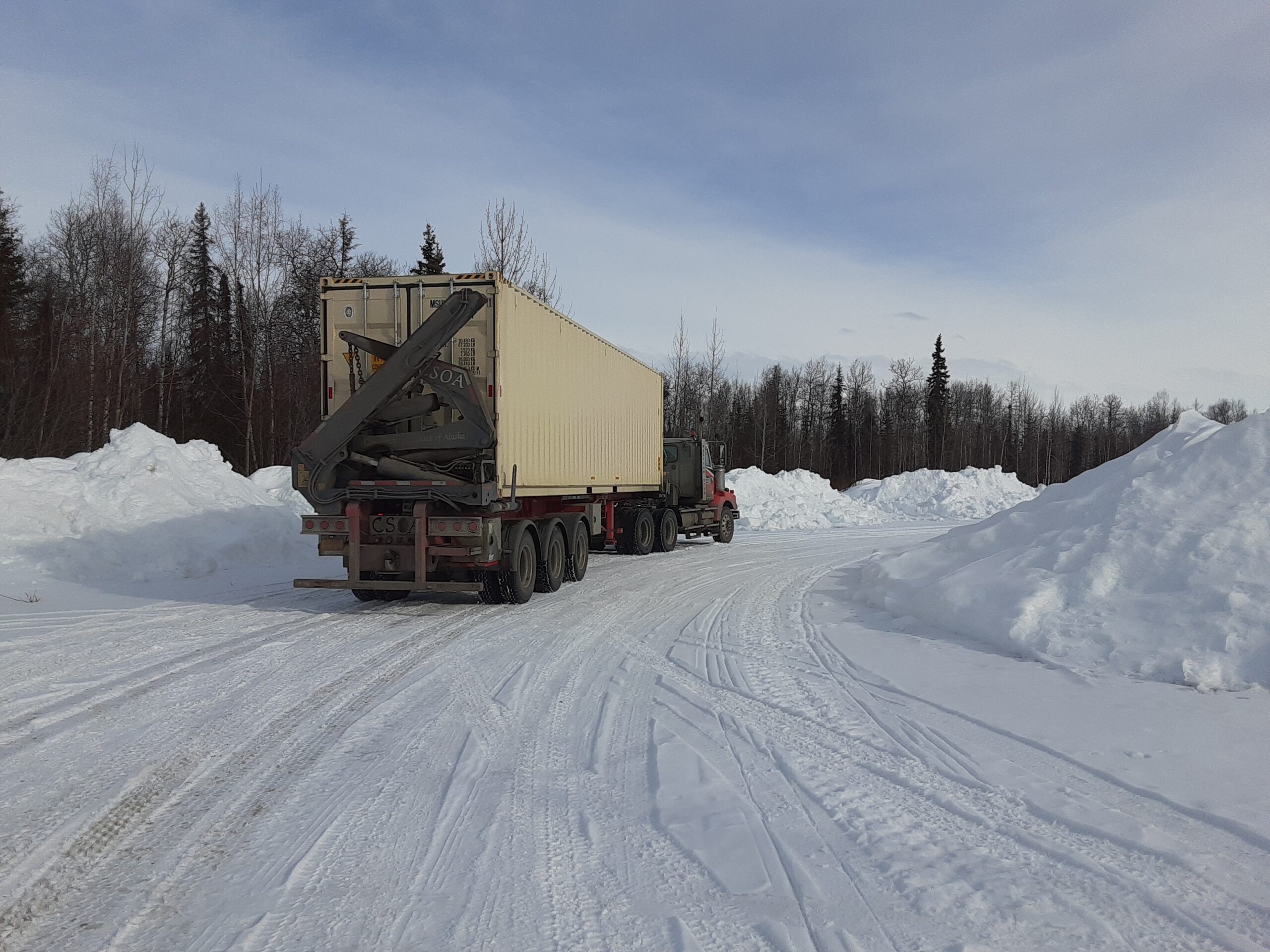
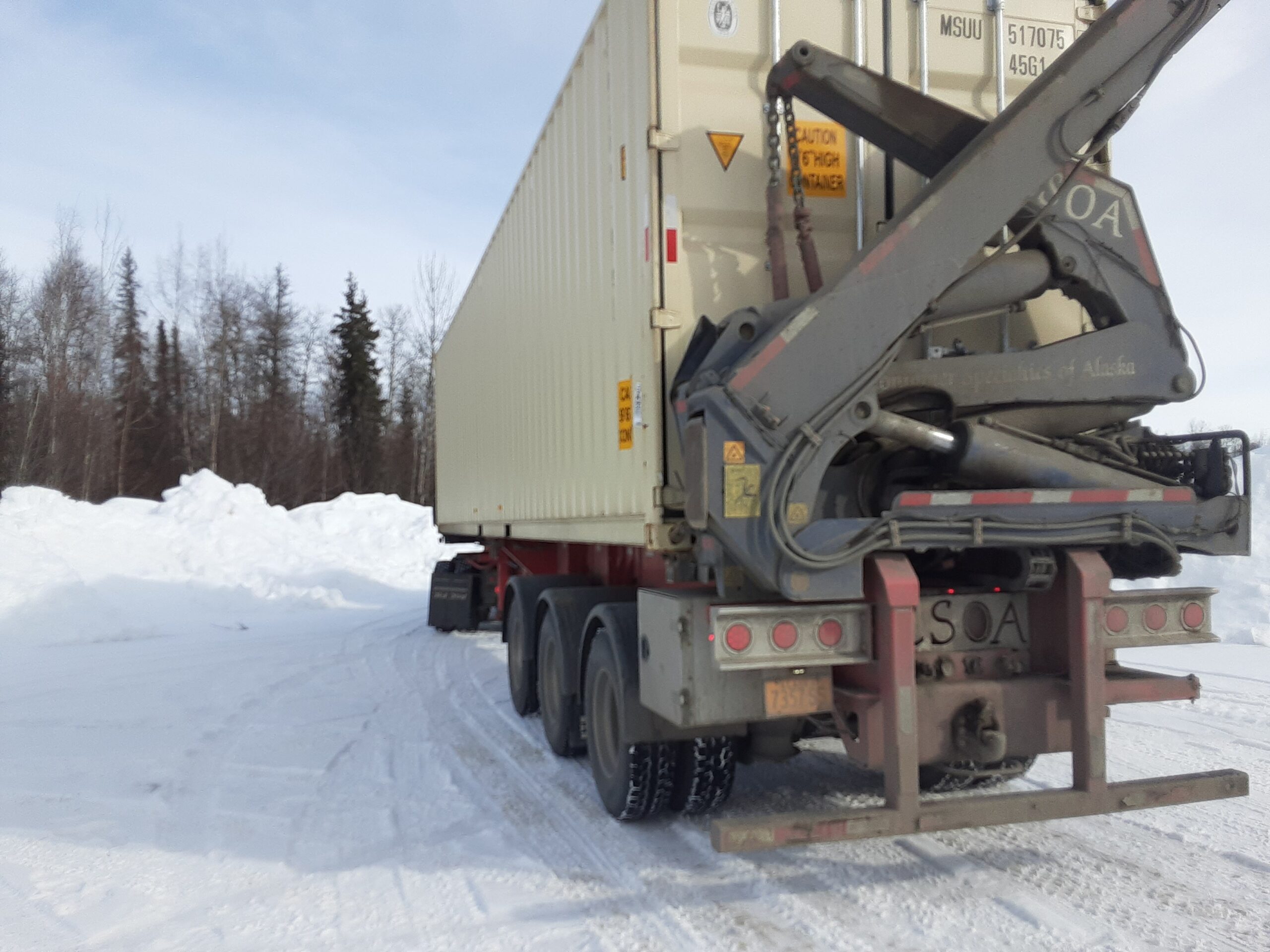
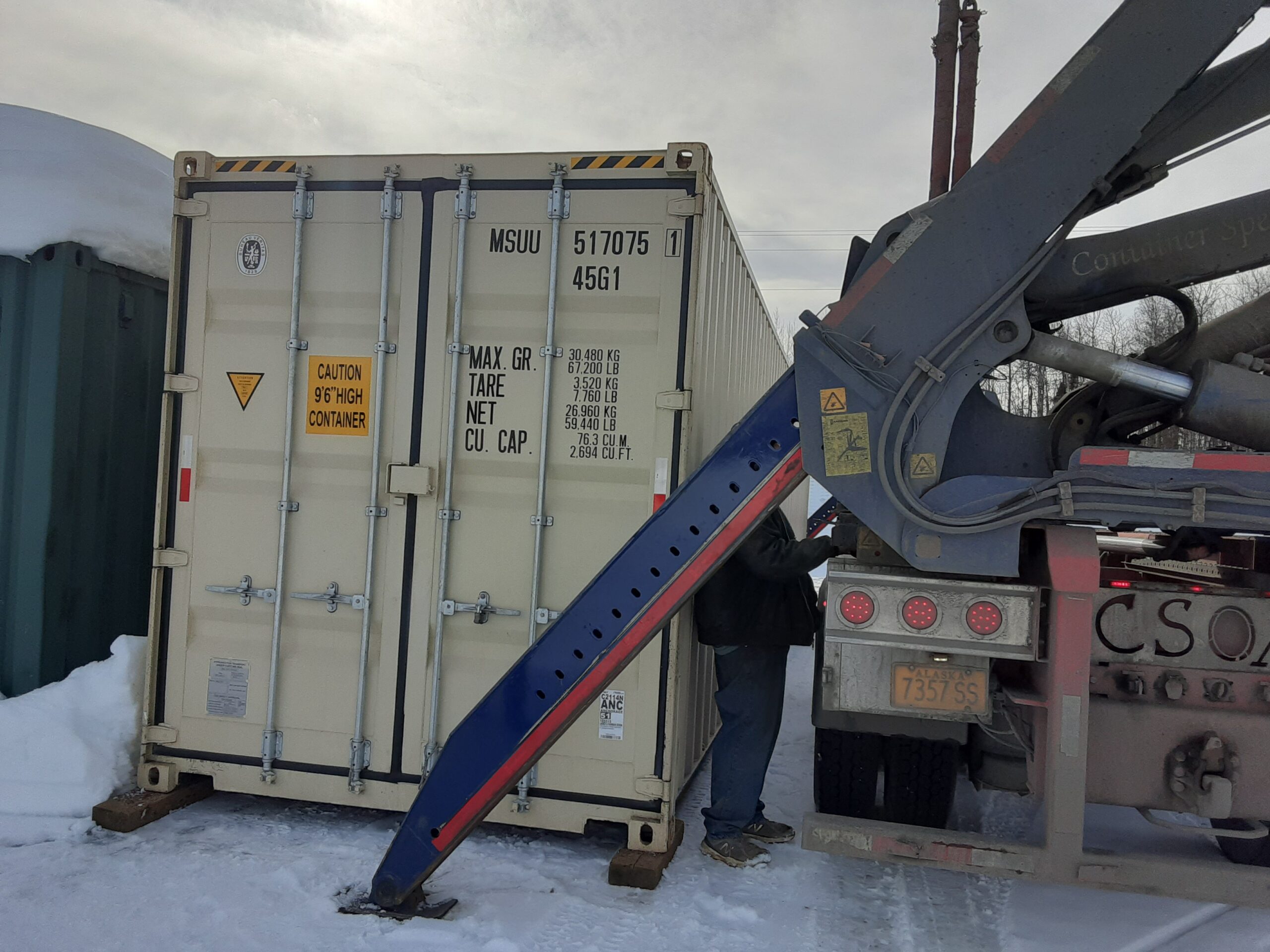
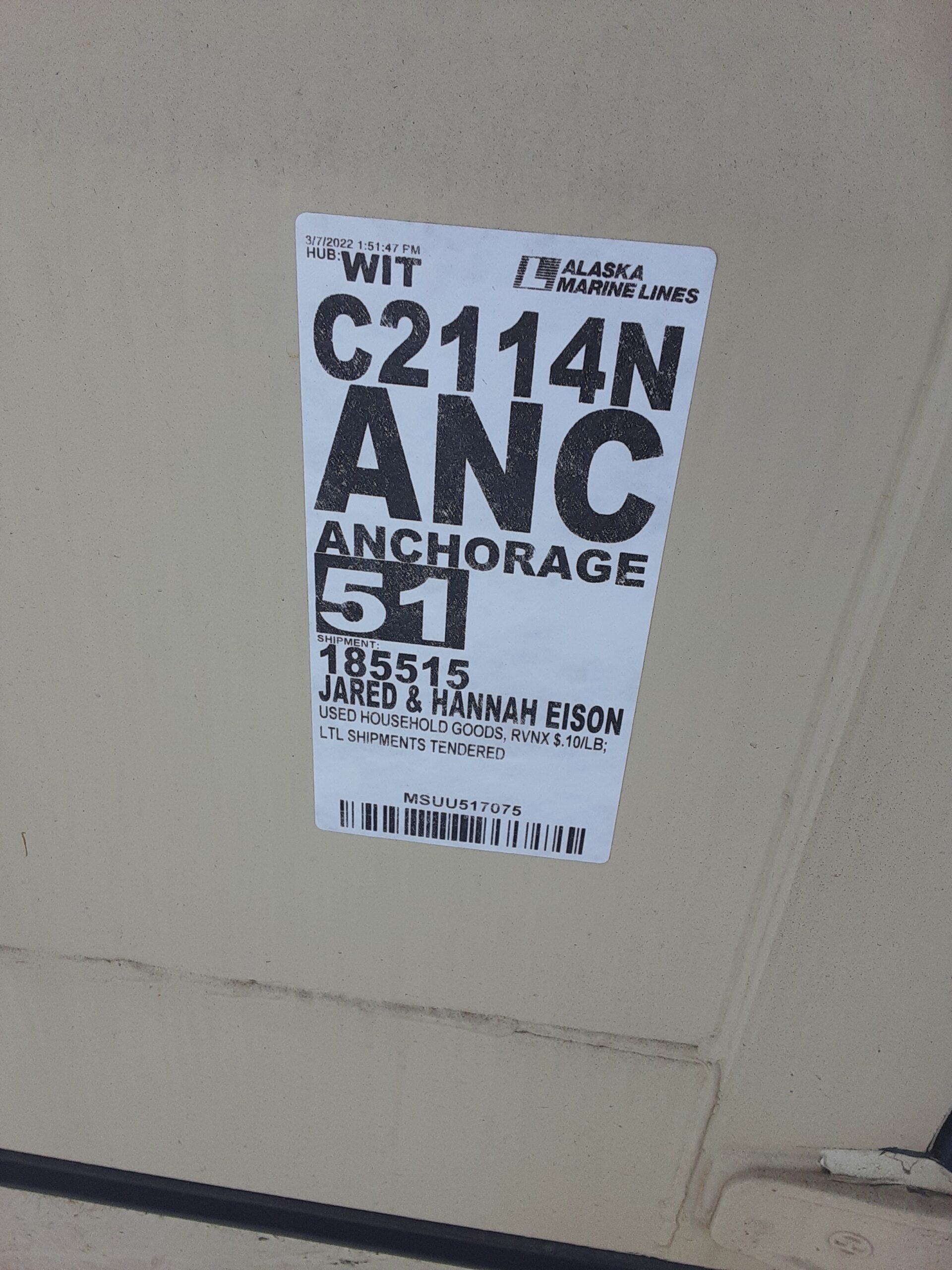
We had three days to get our container out of the Alaska Marine Lines yard so we used Container Specialties of Alaska to haul our container to a storage area using their Hammar truck. Alaska Marine lines was awesome to work with and the staff were very helpful. We were still waiting for our house to sell so that we could buy a house in Alaska so we didn’t have a final place to ship it to. Once we buy a house that will pick it back up and haul it to our new house if it needs it for a storage unit after it is unpacked. Large items such as containers are more expensive in Alaska so we could sell it for more than we paid for it if we end up not keeping it. Storing the container at a storage facility was very reasonable as it is essentially its own storage unit so you are not renting actual indoor storage space.
There are many variables and different needs for people moving to Alaska and this is the option and route we chose that fit us best. We will be living in rural (AKA remote in the lower 48) Alaska so extra tools and parts are a necessity for that. Overall shipping the 40’ container was under two-thirds of the price that using a 28’ semi-trailer would have been and we got twice the storage space with the extra height and length along with having more than three-days to load or unload it so that was the best moving solution for us.